Are you drowning in manual tasks that eat away your productive hours?
Imagine reclaiming 20+ hours weekly while your business runs more efficiently than ever. The secret? Strategic process automation.
But here’s the challenge: most businesses automate the wrong processes first, wasting thousands of dollars and countless hours on solutions that deliver minimal impact. With 79% of companies reporting time savings from automation and organizations saving an average of $46,000 annually through workflow automation, you can’t afford to miss this opportunity.
In this guide, I’ll share my proven 5-step framework for choosing processes to automate.
I developed it over 10 years ago to help businesses eliminate manual labor while maximizing ROI. You’ll have a clear roadmap to automation success that transforms your entire organization by the end.
What is Process Automation?
Process automation uses technology to perform tasks with minimal human intervention, transforming manual processes into automated workflows.
By leveraging process automation tools and software, businesses can execute repetitive tasks consistently and efficiently, reducing human error while freeing employees to focus on higher-value activities.
Modern business process automation ranges from simple workflow automation that handles repetitive manual tasks to sophisticated systems that manage complex processes across your organization.
The key is identifying which processes to automate for maximum impact.
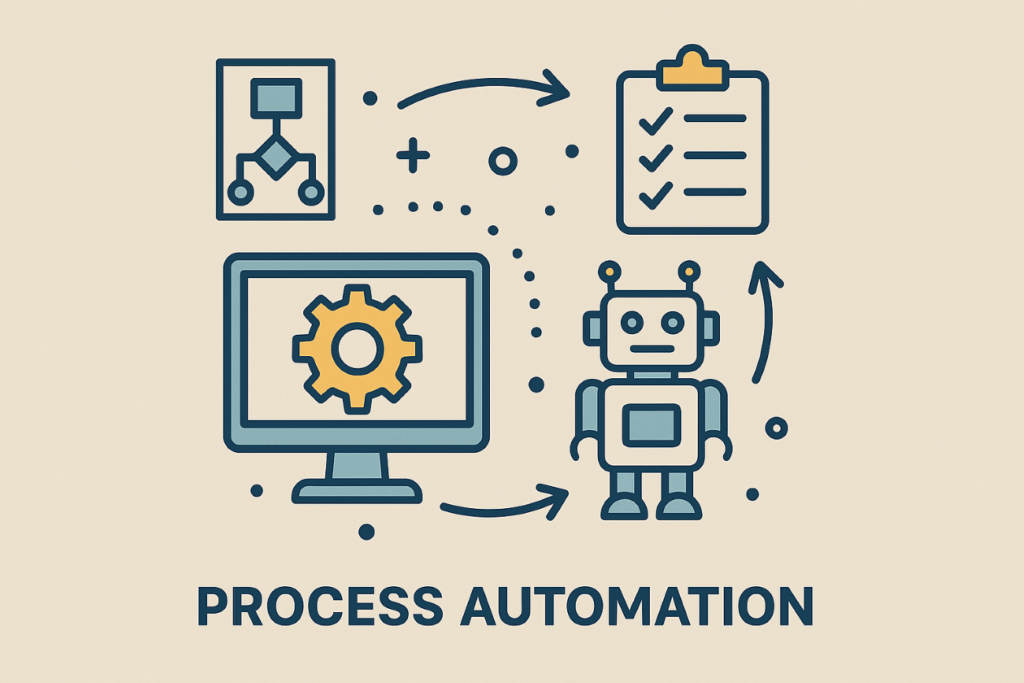
Reasons You Need to Know How to Choose Processes to Automate
In today’s competitive landscape, automation isn’t just nice to have—it’s essential for business growth and maintaining a competitive edge.
-
94% of workers perform repetitive, time-consuming tasks that could be automated
-
Organizations using workflow automation save an average of $46,000 annually
-
90% of knowledge workers report improved job satisfaction after automation implementation
-
50% of work activities could be automated with current technology
-
88% of small businesses say automation allows them to compete with larger enterprises
My 5-step process eliminates the guesswork from choosing processes to automate, ensuring you focus your automation efforts on the areas that will deliver significant benefits with minimal disruption to your business.
Step-by-Step Instructions to Choose Processes to Automate
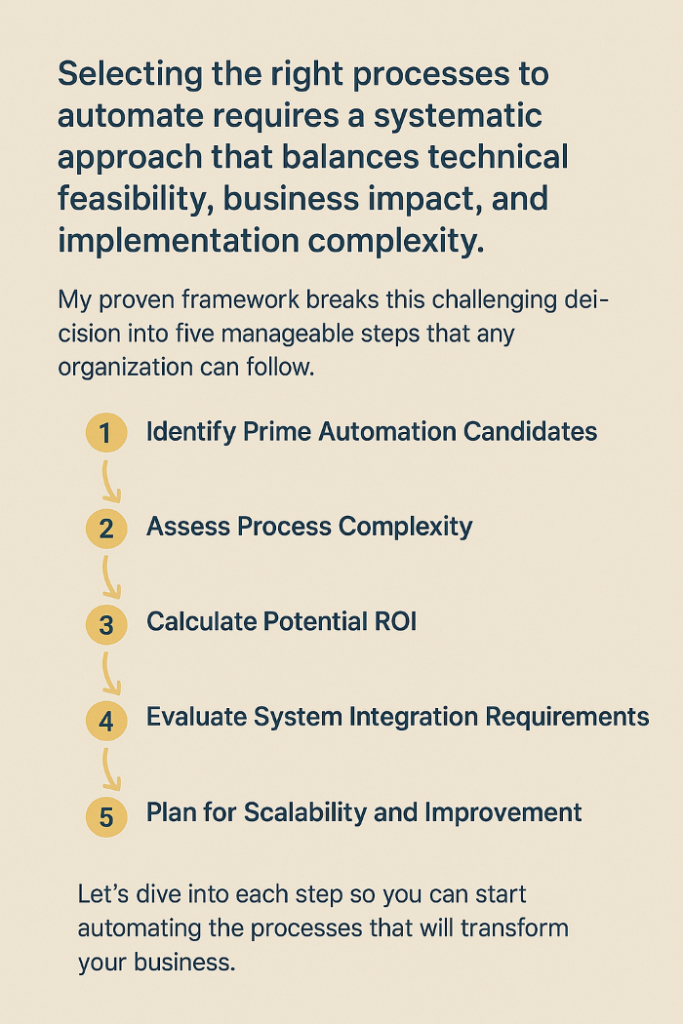
1. Identify Prime Automation Candidates
The most suitable processes for automation are repetitive tasks that occur frequently and follow predictable patterns. These tedious tasks often consume valuable time and are prone to human error.
To identify these prime candidates:
List all processes that your team performs regularly (daily or weekly)
Highlight those that follow standard operating procedures with minimal variation
Prioritize high-volume activities that require significant time
Focus on tasks that don’t require complex decision-making or creativity
According to FlowForma, 84% of businesses successfully automate operational processes first, including data entry, invoice processing, and customer onboarding. These processes typically involve multiple steps but follow consistent rules, making them ideal starting points.
One financial services client identified their invoicing process as a prime candidate. They automated it to reduce processing time by 78% while eliminating errors that previously required hours of correction each week.
2. Assess Process Complexity
Not all processes are equal candidates for automation. Complex processes with numerous exceptions or those requiring significant human judgment may not deliver the expected benefits.
When evaluating process complexity:
-
Document the current process workflow with all decision points
-
Count the number of exceptions or exceptional cases handled monthly
-
Assess the level of human judgment required
-
Consider regulatory compliance requirements (essential in regulated industries)
Simple, rule-based tasks with few variations are automation gold. The more complex a process becomes, the more customization your business automation solution will require, potentially eroding ROI.
From my experience helping a healthcare provider automate their patient intake process, we discovered that while 80% of the process followed standard rules, the remaining 20% required clinical judgment.
They achieved significant time savings by automating only the standardized portions while maintaining quality care.
3. Calculate Potential ROI
Every automation initiative should deliver measurable returns. Calculating ROI helps prioritize which processes to automate first based on data-driven decisions.
To determine potential ROI:
-
Measure current process costs (labor hours × hourly rate)
-
Add error-related expenses (corrections, customer service issues)
-
Estimate implementation costs (software, configuration, training)
-
Project ongoing maintenance requirements
-
Calculate time-to-value (how quickly benefits will materialize)
One manufacturing client discovered that automating their quality control data analysis would save 15 hours weekly and reduce errors by 92%, delivering complete ROI within 4 months.
Focus your automation efforts on processes where the potential cost savings and error reduction outweigh implementation expenses.
This data-driven approach ensures your automation strategy delivers maximum impact.
4. Evaluate System Integration Requirements
The best automation solutions complement your existing technology ecosystem rather than creating disparate systems that increase complexity.
When assessing integration requirements:
Inventory all systems the process currently touches
Document data exchange requirements
Evaluate API availability and quality
Consider legacy systems compatibility
Assess security and compliance implications
Integration challenges can quickly derail automation project management tools. I’ve seen organizations waste thousands on automation tools that created more problems than solved due to poor integration with legacy systems.
A retail client successfully automated their inventory management by selecting a low-code automation platform that seamlessly connected with their existing ERP system.
This integration eliminated manual data entry while maintaining data integrity across systems.
5. Plan for Scalability and Improvement
Effective automation evolves with your business. The processes you automate today will likely change as your organization grows and customer expectations evolve.
To ensure long-term success:
-
Select solutions that scale with transaction volumes
-
Build in measurement and monitoring capabilities
-
Plan for regular review and optimization
-
Document thoroughly for knowledge transfer
-
Consider future integration needs
Automation is not a “set-it-and-forget-it” solution. The International Federation of Robotics predicts a 14% annual increase in automated jobs, reflecting how quickly this technology evolves. Your strategy must adapt accordingly.
One of my e-commerce clients initially automated their order processing for 500 orders daily. By selecting a scalable solution, they seamlessly handled 10× growth over three years without significant additional investment.
Key Considerations For Successfully Choosing Processes to Automate
Beyond the five-step framework, several additional factors can significantly impact your automation success. Organizations that achieve the most significant benefits from automation focus on customer impact, employee adoption, and incremental implementation.
When selecting processes to automate, consider how each potential project affects customer experience. Sometimes automating customer-facing processes delivers benefits beyond efficiency, including improved customer satisfaction and loyalty.
However, it’s crucial to maintain the human touch where it matters most.
Employee buy-in is equally important. The best automation candidates are often the tasks your team members find most tedious and would gladly relinquish. Involving stakeholders immediately ensures your automation efforts address pain points rather than creating new challenges.
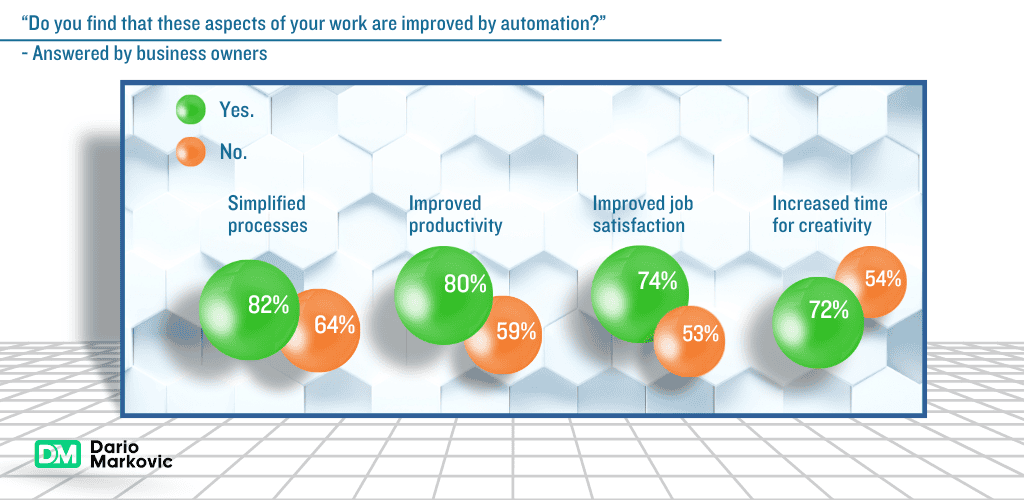
Taking it to the Next Level: How to Build an Enterprise Automation Strategy
Once you’ve successfully automated your first few processes, it takes time to develop a comprehensive automation strategy that transforms your entire organization.
Leading companies are moving beyond isolated automation projects toward an enterprise approach that coordinates automation efforts across departments. This approach requires establishing an Automation Center of Excellence that standardizes methodologies, shares best practices and prioritizes initiatives based on organizational goals.
Data-driven decision-making becomes even more critical at the enterprise level. By tracking detailed metrics on each automated process, you can continuously refine your selection criteria and implementation approach. Organizations with mature automation strategies typically achieve 3-5× greater ROI than those pursuing ad hoc projects.
Consider developing automation capabilities internally through low-code platforms that empower citizen developers.
This approach accelerates implementation while building valuable institutional knowledge.
Alternatives to Process Automation
While process automation delivers significant benefits, it’s not always the right solution. Process reengineering may provide better results with less investment.
Before automating any process, consider whether the current workflow is optimal. Automating an inefficient process merely makes it consistently inefficient. I’ve worked with numerous clients who achieved more excellent benefits by streamlining their processes before applying automation technology.
For processes with high variability or that require significant human judgment, augmentation rather than automation may be more appropriate. These hybrid approaches use technology to support human decision-makers rather than replace them entirely, often delivering better outcomes for complex situations.
Finally, outsourcing remains a viable alternative for some processes, particularly those requiring specialized expertise but limited volume. Weighing these alternatives ensures you select the most appropriate approach for each business challenge.
My Experience With Process Automation
Choosing processes to automate is the most critical decision in your automation journey. By following my five-step framework—identifying prime candidates, assessing complexity, calculating ROI, evaluating integration requirements, and planning for scalability—you’ll focus your automation efforts where they deliver maximum impact.
Over my 10 years guiding businesses through automation initiatives, I’ve seen firsthand how strategic process selection transforms organizations. Companies that methodically choose processes to automate consistently outperform those that rush into automation without proper evaluation.
One manufacturing client increased productivity by 37% while reducing errors by 92% by automating just three key processes. A financial services firm eliminated 2,800 hours of manual data entry annually. These results aren’t anomalies but achievable when you select the right processes using a structured approach.
As you begin your automation journey, remember that choosing processes to automate isn’t about technology but business transformation.
Start small, measure thoroughly, and build on your successes.
The efficiency, cost savings, and competitive advantage you’ll gain are well worth the effort.
Check out the best small business automation tools to build automated processes:
FAQ
What types of business processes are best suited for automation?
Repetitive, rule-based tasks that occur frequently and have predictable outcomes make ideal automation candidates.
Examples include data entry, invoice processing, report generation, inventory management, and standardized customer communications.
How do I prioritize which business processes to automate first?
I prioritize based on a combination of implementation ease and potential impact. I look for “low-hanging fruit”—processes that offer significant time savings or error reduction while being relatively straightforward to automate.
I calculate the ROI for each candidate to create an objective ranking.
What are the signs that a business process might be too complex to automate?
Business processes requiring significant human judgment, handling numerous exceptions, or changing frequently may not be ideal for automation.
If more than 20% of cases require special handling or if business rules change monthly, consider partial automation or process redesign first.
How much can I expect to save by automating business processes?
Organizations typically save 40-75% of the time previously spent on manual processes. According to industry data, businesses save an average of $46,000 annually through workflow automation, with ROI typically achieved within 6-12 months for well-chosen business processes.
How does process automation impact employees?
When appropriately implemented, automation eliminates tedious tasks and allows employees to focus on higher-value work.
Studies show that 90% of knowledge workers report improved job satisfaction when routine tasks are automated. The key is transparent communication about how automation will change workflows.